clbd39
Junior Member

Posts: 79
|
Post by clbd39 on Jan 15, 2014 12:32:18 GMT -6
A NASIOC member and myself put this write up together a few years ago... figured I might as well post it in here (I haven't made a fiberglass box in about a year, but I'm itching to do some more!!) This is a How: To FAQ on how to make a fiberglass sub enclosure. I did not make it specific to any particular type as they all follow the same general rules. I have put in specific information for each major type (side mount, spare tire mount), but if you have any info to add based on your own experience please let me know, PM it to me and I will add it in where it should go (with proper credit or course). If you notice mistakes inconsistencies etc…bring it to my attention please. Building a fiberglass enclosure takes time, money, and patience. On average you are looking at a cost of $200 to properly build one and can spend anywhere from 3-7 days working 6-8 hours a day (depending on curing time etc…). In other words it’s a serious investment. This will be a great experience and give you something to do to get away from the wife/girlfriend as you’ll smell so bad from resin they won’t want to get near you while you are working on it J You will need the following supplies and equipment. The majority of supplies can be found at www.uscomposites.comThere prices are VERY good even taking into account shipping and you can get all the supplies you’ll need from them. If you go with them make sure to use their premium lay up resin as it is good for vertical walls. Also, your fiberglass/resin materials will be polyester based as Epoxy based fiberglass products take much more effort to properly use and are much more expensive. Supplies needed Resin (2 gallons is usually the minimum) Use a premium lay up resin if possible Hardener MEKP is what you’ll be using. Fiberglass mat (3/4 oz. and 1 1/2 oz.) Depending on how many curves you may need 2-5 yards of each. Fleece (a few square yards) Paint brushes (to spread the resin) Mixing sticks (I used tongue depressors) Used to mix up resin Mixing cups (use one that don’t have a wax coating…preferably plastic) Chemical mask with filters (EXTREMELY IMPORTANT Experienced member had a seizure from not being in a mask with the correct filters) Latex gloves (LOTS) Body filler (Rage Gold Extreme if you can. It is the most easily sandable) Plastic spreaders (for body filler) 3/4” MDF Dowel rods (not needed, but it’s nice) Sand paper with multiple grits from 36 on up to 2000 possibly. Equipment needed (you don’t NEED it, but it makes life so much easier) Router with circle jig and appropriate bits Electric stapler Dremel with cutoff wheels or carbide cut off disk Air compressor, air saw, sander, and air blower Saw zaw (if you don’t have an air saw).
|
|
clbd39
Junior Member

Posts: 79
|
Post by clbd39 on Jan 15, 2014 12:32:29 GMT -6
General rules of fiberglassing.
1) Personally, because of wanting to protect my sub, be it a side enclosure or spare tire well enclosure I make a “double baffle”. I cut a ring with an opening the size of my sub, and anther ring that will fit around the outside of my sub and attach them together. I use 3/4” MDF for this so keep in mind you’ll have a 1 1/2” thick piece of MDF. By doing this you can recess your sub and put a grill over top of it, or custom make a cover. It looks nice, and gives you added protection. Pics #4-#6 show this is good detail. If you’re building a spare tire enclosure this is a good way to gauge the height you’ll need for your false floor or the distance you have to work with if you are going to try and keep it the same height as the stock floor.
2) Take your time and don’t rush. Mixing resin and hardener in a 1% to 2% ratio will give you anywhere from 15-30 minutes of working time before it begins to gel (depending on temperature). Don’t mix up a batch of resin with a super high hardener percentage as that could cause your structure t warp. In other words, if you don’t have the time to do it right then don’t bother…you’ll screw it up.
3) Prep your car. Put down plastic over all the fender, bumper etc…if you don’t YOU WILL get resin on the vehicle (ask someone who knows ARGH!!!!).
4) If possible do it outside or in a garage with an open door. If you have pets try and keep an eye on them, and same thing with small kids. This stuff is nasty and you don’t want either the pets or the kid’s touching/eating this stuff.
5) Wear OLD CLOTHES and make sure you wear long sleeves even in the summer. Fiberglass strands will get in your pores and itch like a fiend. If this happens take a really cold shower and wash a couple of times with soap and a scrub brush. Eye protection is also needed.
6) Sand outside in an area without wind. You will get dust everywhere and you don’t want to piss off the neighbors (if you do make sure you sand near them he he).
|
|
clbd39
Junior Member

Posts: 79
|
Post by clbd39 on Jan 15, 2014 12:32:43 GMT -6
Step 1
Mask the area you plan on fiberglassing with masking tape (Pic #1, although I mask the entire area, not just the outline as you will understand soon). Many people have used blue or green painters tape, as well as standard masking tape. In any case make sure to put down two layers of tape overlapping the seams. This will help create a waterproof shield. Also it is imperative to mask out an area quite a bit larger than what you will actually lay the fiberglass on. The reasoning is simply for protection of your car from spills, dripping etc… Once you have the tape placed use some adhesive spray and put aluminum foil overtop (Pic #2 I personally use adhesive spray to hold the foil, clbd39 uses tape as seen in his pic More exposed foil makes it easier to remove the fiberglass). The key here is to make the aluminum foil as smooth as possible and overlap seams (also you can tape that seam down, but I don’t bother). Use a roller or plastic spreader to flatten it out. If you tear it either try and patch it with the foil already there, or replace it…don’t put down another small piece…it will just create even more seams and possibly move during the fiberglassing step. If you can use the industrial strength stuff found in restaurants, as it’ll resist tearing more than the standard stuff in the grocery store.
Step 2
Start with 3/4 oz. Mat cut/tear it into small 2”x2” pieces and use spray adhesive to tack it to the aluminum foil. This will help keep it upright while applying resin. I like to cut it into long strips and then rip it apart as the torn edges work better to conform to corners and by overlapping pieces you will still build up thickness quickly without having to spend precious minutes trying to knock out air bubbles. I would go at least 2-4 inches outside the max area you plan on using. The reason for this is to make sure you get a good thickness at what will be your edge (again, make sure you taped/foiled a large enough area). Once you have a layer of mat “glued” start with the resin. Mixing resin is critical, so if it’s your first time on a particular day mix up a small batch to test it’s working time, and curing time. If you use too much hardener it will cure to quickly, warp and you’re screwed. To little hardener and it may never fully harden or take days and days to do so. If I can get 15-30 minutes of working time from the resin before it begins to gel than I know I have a good resin/hardener ratio. It is best to use the minimum amount of resin needed to soak the mat, as extra resin does not add strength. Resin by itself is extremely brittle and will break easily. Use your brush to tap out any air bubbles that form. Air is your enemy when building up layers as it creates weak points in the fiberglass. Before the first layer has a chance to cure start placing more layers on top. I use a combination of 3/4 oz. and 1 1/2 oz. mat to help build up layers quickly. 3/4 oz. mat is better in corners where you have trouble getting mat to conform. Some people will say it’s fine to let each layer of mat cure before putting the next one. I disagree, as I want as many layers to intertwine with each other to increase strength. Also it is key to ONLY use as much resin as needed to soak the mat through. I cannot stress this enough. If you think you might have too much resin down just lay more mat on top and wait a minute or two…if it starts to soak up then you know…if it doesn’t, then add a small amount of resin. Continue this until you have at MINIMUM 1/4” thickness. I would try to shoot for 3/8” myself and if you are using a large sub shoot for 1/2” thickness. You need a uniform thickness as well so don’t have it 1/8” at one spot and an inch in others. Once you reach the thickness you desire let the mess you’ve created cure overnight. Pic #3 is a great shot of what this step will look like.
Step 3
Once you’ve let it cure overnight it’s time to pull it out of the vehicle. This should be easy as the aluminum foil will pull right away from the tape and also leave the back of the enclosure nice and smooth. If it’s stuck pull carefully until it pops out. This is why all the prep work is the important step. Once you have it removed use a marker and draw the line where you want to cut the excess material off the enclosure. It is VERY helpful to have a saw zaw, an air saw or the very least a dremel with a carbide cutting disk. If you don’t have this stuff…go out and buy one of them QUICK (Pic #12). After you have cut off the excess use some sort of power sander with 36 grit (I like an air pressure based orbital sander to make quick work of the sanding) and clean up the edges by rounding them over. Slightly. Also, clean up an inch to two inches of the area near the edges with the sander to remove the waxy-like finish on the fiberglassed material. This will help the next portion of fiberglass bond well to the base. Clean up your enclosure at this point with some alcohol and water and a sponge. Some consider this excessive, but I like to remove as much dust as possible from the inside and clean up the soon to be bonded edges to increase strength even if it is a slight amount. If you are going to just use an MDF board for the rest of the enclosure go to step 4a, if you are going to use fiberglass go to step 4b.
|
|
clbd39
Junior Member

Posts: 79
|
Post by clbd39 on Jan 15, 2014 12:33:20 GMT -6
Step 4a
Take a piece of cardboard and make yourself a template of your baffle/front of the enclosure using the part you just fiberglassed as a guide. I would make it one piece and try to get it at as exact as possible to the dimensions of the enclosure. Once you have it to where you think it is accurate transfer the template to a 3/4” piece of MDF and cut it out. Secure it to the enclosure with fiberglass and resin. You do not need to make it 1/4” at the seam on the outside, but I would shoot for 1/8” if possible and try to hit 1/4”. You will put mat/resin on the inside of the enclosure to finish up strengthening this area. The issue if you build up the thickness too much on the outside it might not fit back into the area that you made the enclosure for. You will still end up with a minimum 1/4” thickness, it’s just a bit harder to do. After securing the baffle to the enclosure retest fit it and make sure you didn’t build up the outside too much. If you did, just sand it down until it fits and make sure to build up on the inside with a larger quantity than you would have otherwise. The seam is always the weakest point in an enclosure so keep this in mind.
Step 4b
Create a baffle from 3/4” MDF with a router slightly larger than the sub itself (I usually shoot for an extra inch on the radius…so a 12” sub I’d cut out roughly a 13-14” diameter baffle). Cut out the center for the sub to fit into at this point as well. What I do, and many consider it overkill (I don’t) is I rabbit a 1/4” lip around the outside of the baffle. Why this is done will be explained soon. Once you have the baffle created use wooden dowel rods, or small pieces of scrap MDF to set/support/angle the baffle onto the enclosure how you want it to be. I use superglue with a CA accelerator to lock it into place faster. Once it’s in place I then mix up a small batch of resin and use some left over mat and just reinforce all the supports to make sure it’s not going to fall apart when I stretch the fleece.
Once that is done I stretch my fleece over the enclosure and staple it to the rabbited lip on the baffle. Make sure you have enough fleece to reach all the edges after you’ve stapled the center of it to the baffle. Once it is stapled to the areas it needs to be I then continue to stretch it and use adhesive spray to glue it to the sides of the enclosure. The key here is to try and make the fleece as smooth as possible as this will really help in the finishing steps. After everything is glued/stapled I get a nice sharp razorblade and cut away the fleece covering the baffle all the way to the staples. I then grab some painter’s tape, cover up the exposed MDF and opening of the baffle and then glue down some more aluminum foil over the top. This keeps crap from getting over the baffle and ruining your day later. Make sure that you’ve only covered the TOP of the baffle. You want to leave as much of the lip exposed to give the fiberglass something to bond to.
From this point on break out a ton of resin, mix up some batches and start soaking the mofo out of the fleece. DO NOT resin the sides you glued down. It will break the adhesive down and cause your fleece to fall off. You will use quite a bit of resin here, and probably think you’re using too much. Chances are your not, and you’re actually under the amount you need. One way to figure out how close you are is if you start to see it pool on the surface of the fleece a few minutes after you soaked that area then you have probably saturated that spot. If you don’t see that add more resin over those problem areas. Once you’ve done this step let it cure until stiff and then hit the sides of the fleece. You don’t need it to be fully cured, but the more the better. After that step let it cure for a few hours or overnight.
After you’ve let it cure use your sander again and take off that waxy-like film. You don’t have to have this perfect, but it does help things. Again, clean it with some alcohol/water and s sponge and let it dry. Start laying up your mat at this point again, shoot for at LEAST 1/4” thickness. Now, some of you will go “why the hell do I need to do this? I just put down this huge thick piece of fleece?” The problem is fleece is not very strong and is actually very brittle. I found this out firsthand by pushing on a spot of the fleece on my enclosure and actually broke it…with my pointer finger.
Once you’ve done this let it cure again and then remove the tape/foil. Use some more fiberglass and resin to shore up the seams on the inside to make sure you are nice and strong. When it’s all said and done sand down the newly laid exterior fiberglass and clean it.
|
|
clbd39
Junior Member

Posts: 79
|
Post by clbd39 on Jan 15, 2014 12:33:32 GMT -6
Step 5
Break out your body filler and start spreading it out on the enclosure using a plastic spreader. Don’t do too much at once as you want to start sanding it down once it starts getting to a clay-like consistency. This will save you tons of time. Although you can use a power sander I personally use my hand and different sanding blocks. This helps me maintain the shape and get the right feel for the bodywork. You’re going to have to do a couple of layers of filler before you’ll be happy with it. Again, clean it as per the usual steps and let it cure for a few hours.
Step 6
Now you can paint, vinyl, or carpet your box. I’ll break this down for each one to give you more detail.
6a – Painting
If you go this route you need to spend more time on the body filler/sanding steps. Sand, sand, sand. When your hands start to bleed take some Advil and sand some more. Start with the usual 36 grit, and work your way up to 400 grit wet sanding at that point. Once you think you’re good use a high build polyester based primer and…well…primer. Sand down until you have a nice even finish over the enclosure. You can do as many coats as you like, but I try to stay under five. Then hit it with your paint of choice with 3-5 light coats. Sand with the 400 grit wet sand and work up to 2000 grit wet sand. Finish off with a clear coat with 3-5 coats and hit it with a light wet sand of 2000 grit. Buff it up with some polish and you’re set.
If you don’t want to a “wet look” then use some sort of wrinkle paint or textured paint. After you finish the 400 grit wet sand just use that and call it a day.
6b – Vinyl
You need to find a nice vinyl like a 4 way stretch or a heat formable (like that sold by Select Products). You should have already sanded the outside with 36 grit and cleaned it as usual. Use DAP Weldwood contact cement (red, not green) and cover the outside of the enclosure you are going to vinyl, plus the vinyl itself. Let it flash off…a minimum of 15 minutes depending on the temperature. An extra set of hands helps at this point. Try and lay the vinyl where you have the smallest number of wrinkles and work out using a heat gun to form it into the areas you need. Remember that the contact cement is a one time only. You may be able to peel it off once and relay it, but that’s about it. Make sure you keep as much of it from making contact as possible and only push on the area you are trying to adhere. Honestly vinyl is the hardest to do as you can easily screw up and have to start all over. Make sure you know what you’re doing or know someone that does. If you pull up too many times you may rip the body filler out and have to start over. I don’t like to have anything but MDF or body filler directly under where I’m mounting my sub as with a smoother surface it’s easier to seal with the rubber gasket. I usually place the sub and mark where the vinyl is covering it and cut it slightly back so the very edge of the sub is covering the edge of the vinyl. This is an anal nitpicky thing so do it as you see fit.
6c – Carpet
Pretty much follow the same steps as the vinyl. Carpet is a bit more forgiving though so you can play around with it a bit more. Pics #10 and #11 are great shots of how to carpet. Notice how the sub is not sitting directly on the carpet allowing a good seal.
Step 7
At this point you are pretty much done except mounting the enclosure and running wire. What I do is use banana plugs, drill holes in the enclosure where I want them and epoxy them in place from the back side, Attach the wires for the inside of the box, and epoxy again from the inside. This seals them into place and makes it unlikely for them to pop out. Some may want to use terminal cups though. This is perfectly fine, just make sure to seal it with epoxy or resin to keep it from leaking air. As for mounting it depends on application
|
|
clbd39
Junior Member

Posts: 79
|
Post by clbd39 on Jan 15, 2014 12:33:43 GMT -6
Application specific mentions
Side Enclosure
Mounting this can be a bit hard. There are a few openings already in the car on both sides you can use. I mounted mine on the drivers’ side and used an existing hole next to the jack entrance. I just removed the trim panel clip and drilled a hole through my enclosure at that same point, and mounted it. As you can guess that really isn’t enough. There is also an unused hole UNDERNEATH the carpet. I was not aware of this, but it is a great idea. The only negative with that one Is the bolt is expose to the outside of the vehicle so make sure to hit it with some sort of rubber sealant or paint. I also made a mount by screwing a piece of 1/2” MDF to the sheet metal right next to the rear light assembly with a T-nut in it. Drilled a hole through the enclosure to that point and bolted it into place. Make sure you hit these bolts with silicone sealant from the inside of the enclosure to make them airtight. Also, remember the trunk arms. You’re going to have to angle part of your enclosure to keep from hitting the bar. I made an MDF skeleton curved like I wanted it to look like and stapled the fleece to it when I was on that step, then used body filler to smooth it out and flow.
Spare-Tire Enclosure
If you leave your spare in you might be short on room unless you use a shallow mount sub, or a smaller unit. Even if you remove the tire some subs might not have enough depth to be placed in taking into account distance needed behind the sub (JL Audio subs require at least one inch behind the sub for the pole vent). To combat this you can build a false floor using MDF, plywood, etc…to raise up floor to the amount of room you need. By doing this you also can mount your amps down below it leaving almost your entire trunk usable. It is also a good idea to use a false floor to keep the sub BELOW the level of the floor. This will allow you to make a cover to keep the sub from being damaged and keep it hidden (key for wagon owners). Securing this enclosure is pretty easy. Basically drill a hole where the stock mounting location is, and use a bolt to lock it down into place, again with silicone to seal it. If you are going to leave the spare tire in place you’re going to have to still secure it the same way (unless you use a false floor) and therefore it is a good idea to keep a screwdriver and the proper bit to remove the sub from the box so you can get to the mounting bolt. If anyone has a better idea how to mount while keeping the spare please share with me.
|
|
clbd39
Junior Member

Posts: 79
|
Post by clbd39 on Jan 15, 2014 12:34:05 GMT -6
Side Box(Pic #1) Taping (Pic #2) Tom Foil (Pic #3) Fiberglass applied (Pic #4) Circles cut for flush mounted rings (Pic #5) Rings cut and screwed together for flush mount (pic taken for 2 boxes, one on either side) (Pic #5b)Sub is flush mounted
|
|
clbd39
Junior Member

Posts: 79
|
Post by clbd39 on Jan 15, 2014 12:34:19 GMT -6
(Pic #6) Mock sub to make sure there is atleast an inch behind the magnet before mounting (Pic #7) Ring mounted with trunk arm clearing mock (removed after front is glassed) Another version Pic #7b (Pic #8) Cloth pulled over the front before puting resin on it (Pic #9) Put in car to check for clearance of trunk arm and for fitment check (Pic #10) In the car after carpeting (Pic #11) Finished product 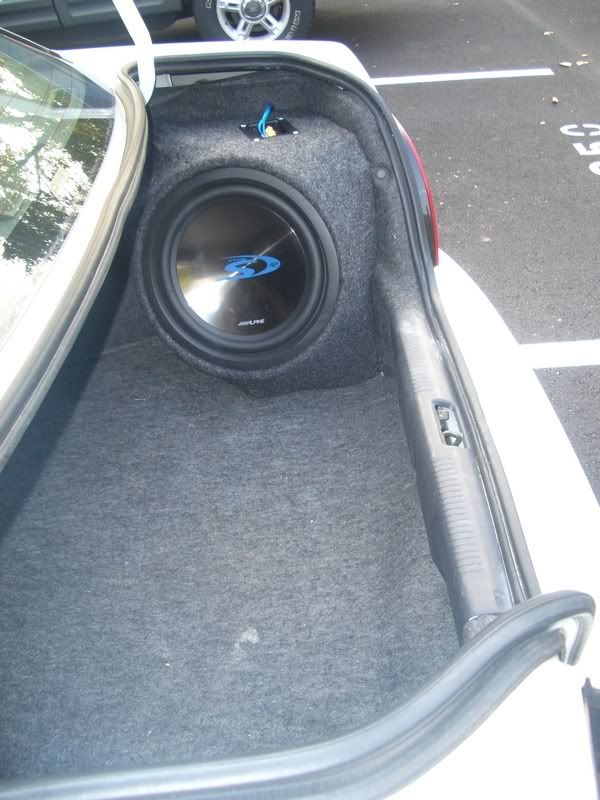
|
|
|
mulder
Junior Member

Posts: 95
|
Post by mulder on Jan 15, 2014 14:50:12 GMT -6
I'm liking where the sub goes in the corner of the trunk. I should have you make one for my type R 10 inch sub
|
|
|
Post by Deleted on Jan 15, 2014 17:44:26 GMT -6
This thread is now a STICKY! Great write-up dude! Anyone with material suggestions and/or design suggestions post up! I came across some UV curing resins not too long ago after following Steve Meade Designs on Youtube. Great stuff. If I come across some money to build I'll definitely hit you up. I'd be eager to learn this for sure! I've got 2 x 12" JL 12w3v2 subs and a 500/1 monoblock I've been looking at putting in my car, but want to save weight if at all possible. Probably will trade for a couple 10's or or just use one 12" with a good enclosure. Either way, just lookin for some bass that I've missed for so long! HA! Link to SMD SunFlash UV curing resin
|
|
clbd39
Junior Member

Posts: 79
|
Post by clbd39 on Jan 16, 2014 11:16:15 GMT -6
I'd be happy to build or help out. I used to buy my fiberglass mat off eBay, but it has gone up in price quite a bit since, but you just want to make sure you get a decent weight as well. I used to have an RE SX 12 with a directed audio amp sending 1200watts to the sub, in a 2.5cu ft ported box. After that I decided enough is enough, I'm going to just put a small side pocket sub in. Ended up with an Infinity 10" Kappa Perfect with a small RF 350watt amp. I ended up putting the amp under the passenger seat and just have the wires cleanly running through, and plenty of trunk space! 
|
|
mulder
Junior Member

Posts: 95
|
Post by mulder on Jan 16, 2014 12:28:00 GMT -6
what would you charge for a 10 inch sub box to be built?
|
|
clbd39
Junior Member

Posts: 79
|
Post by clbd39 on Mar 17, 2014 11:08:33 GMT -6
Someone was asking me what my own box looks like so why not post it here... Nothing too special just a functional small and clean box holding a 10" Kappa Perfect sub. The amp is under the passenger seat and the wire is just run under the carpet or plastic. Covered in a suede like material I got cheap at a fabric store. Under the fabric I sanded the box, then a thing layer of bondo sanded smooth since the fabric would show EVERYTHING.  
|
|
|
Post by besthaticouldo on Mar 19, 2014 16:24:49 GMT -6
Wanna help me do a fiberglass box? In my trunk?
|
|
clbd39
Junior Member

Posts: 79
|
Post by clbd39 on Apr 1, 2014 11:08:51 GMT -6
Oh sure, you got the supplies?
|
|
|
Post by besthaticouldo on Apr 3, 2014 9:26:18 GMT -6
I will soon, I got the ring and the sub. Need to get a few more things.
|
|